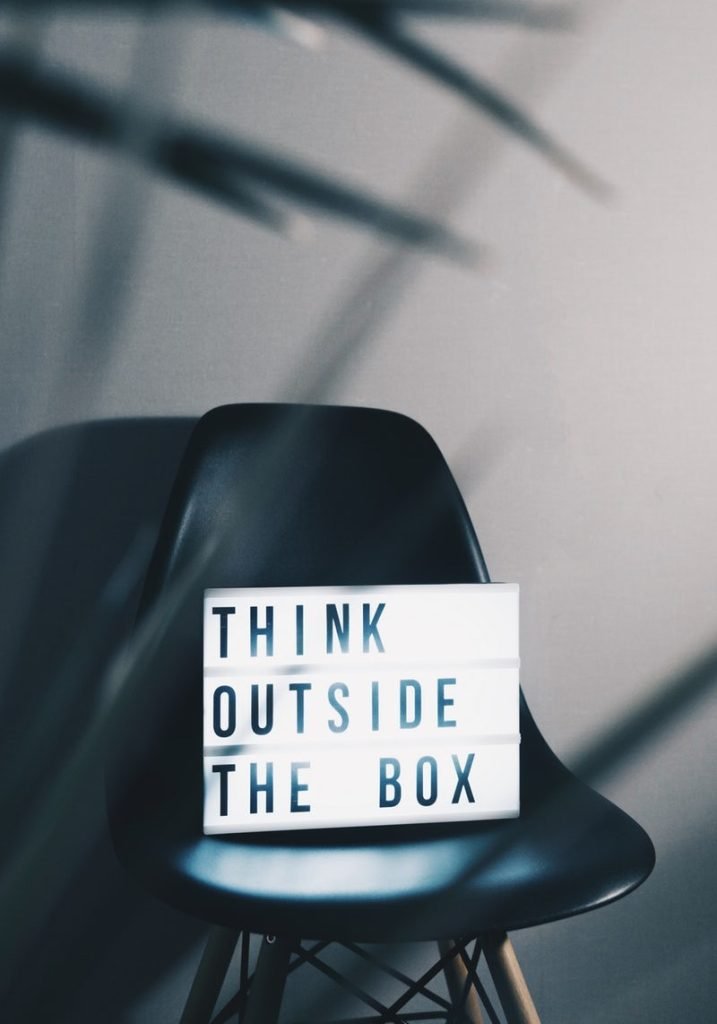
Some projects require field coating, while certain projects must be coated in the field due to mobility and size issues. But all too often, when writing specifications, engineers don’t analyze the situation and instead continue on a path towards defaulting to field coating each time as status quo.
In the world of specialty coatings, we would like to challenge you to think about another option that is a far better choice for certain coating situations: Shop Coating. Each time we are assessing a project, we consider several factors. When deciding whether the job would be optimized through field or shop coating, the very first thing we ask ourselves is, “Are there any parts on this job that could be pre-coated?”
The Project
Deep Rock Tunnel Project is Indianapolis’ solution to improving water quality in area streams while preventing nearly 1 billion gallons of sewage from entering waterways annually. The system is a 28-mile long network of 18-foot diameter deep rock tunnels built 250-feet under the city. Massive amounts of process piping were part a of this project, as DECO applied coating to 48” diameter vertically installed pipes going down over 250 feet.
The Great Debate
We had to first answer the question, “Should we be coating the pipes on the ground at the job site, or in shop?” Coating pipes on the ground present a number of challenges. Indiana weather has a complete four-season weather pattern, including freeze-thaw events (rain, dew, humidity, etc). Another issue we had to battle was an active construction site (construction dust, active WWTP operations, dirt and mud from weather events). We also had construction schedules that permitted a very limited time to apply coating. Other challenges included working around the other trades on site and dealing with limited access to all surface areas of the deep rock tunnel pipe. Schedule delays for any of the above mentioned issues could compromise Quality Control and Quality Assurance.
After considering the option of Field Coating, we turned our thoughts to Shop Application. Coating parts in shop provides a number of things: Quality Control/Quality Assurance controlled environment, no weather delays, no fugitive dust contamination, and yet gives full access to all surface areas. Shop coating also allows for earlier schedule delivery and provides extremely accurate and detailed coating application reports. But before we could make our decision, we had to get a little more in detail as to if and why shop coating would be better in this case.
We realize that each project has different needs and requirements. For example, when coating projects that have pieces too large for transport, the coating needs will be very different from those that may be dismantled and shipped. Everything from surface materials to geographical location affect the way something will be optimally coated. The Deep Rock Tunnel Project was very specific in its needs, so we went through a series of steps to decide whether we should do Field Coating or Shop Coating.
The industry took notice of this innovative project we were involved in, which was incredible because we loved spreading awareness of something that is so environmentally necessary for our city.
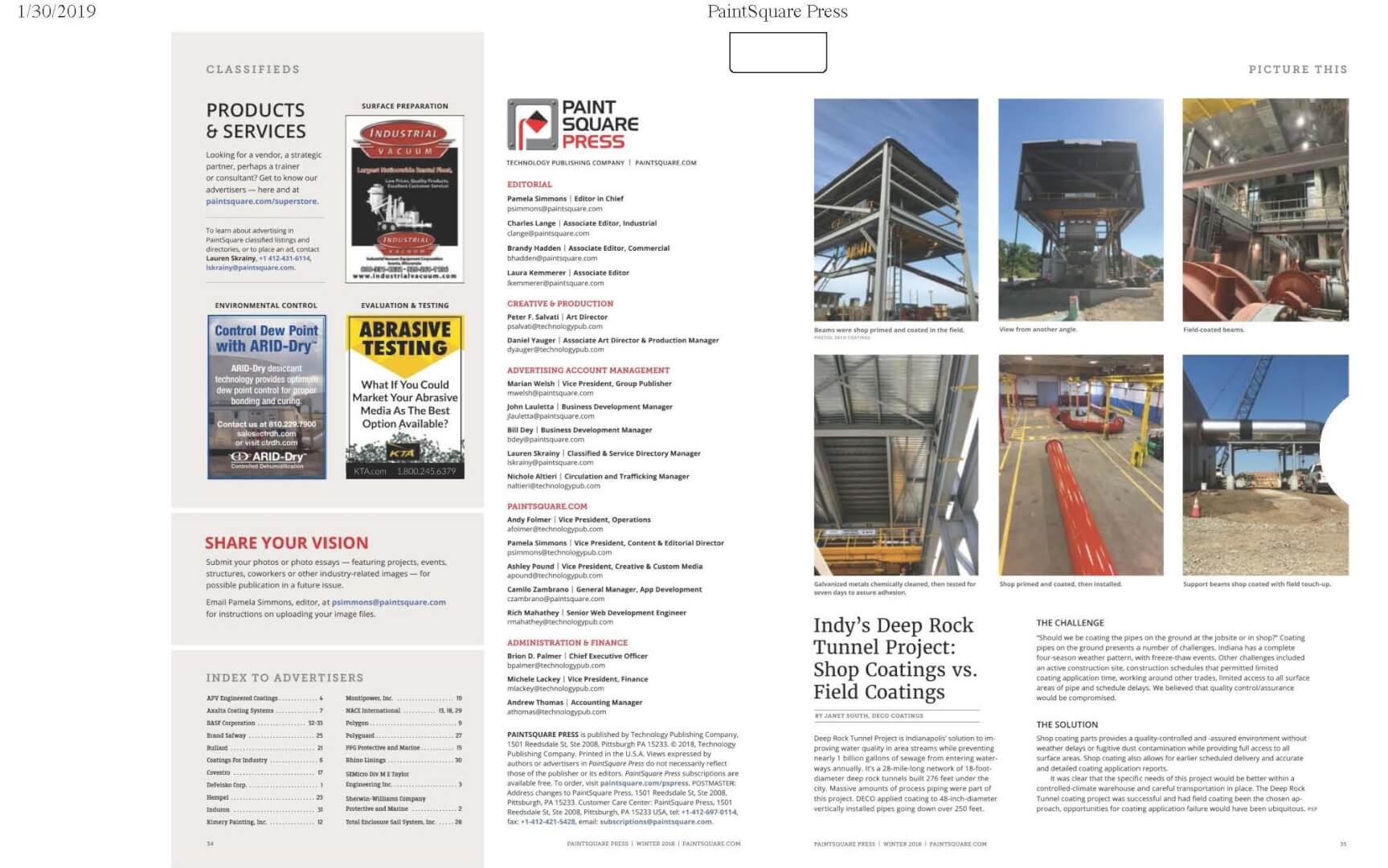
The biggest decision on this project was whether to do it in the field or in the shop. Here are some of the points to consider on coatings projects:
Shop Coating Pros:
- Accelerated schedule. Items arrive pre-finished reduces the need for field painting.
- Reduced safety risk on job. Reduced field painting scope and reduced number of workers onsite exposed.
- More choices of coating products. There are less limitations of site VOC and other environmental conditions.
- Ensure/higher quality control. Most coatings are tested for performance in a lab, so why not apply them in the same controlled conditions?
- No climatic delays. Coatings are all applied in a climate-controlled shop. Weather does not affect the ability to coat at any time.
- Request shop reports from fabrication to final coating. This ensures product compatibility and validates adherence to specification.
- Reduces finger pointing and blame game between spec divisions. There is no room for speculation on what division did what, because when coatings are done in the shop, there is only one place things go good or bad…in the shop!
- No overspray or drips to other trades. Clean up is reduced on entire project.
Shop Coating Cons:
- Freight. Transportation can be additional costs not originally budgeted; however, the early delivery of finished items sidesteps project scope creep.
- Scratching or marring of surfaces. If cured properly, scratching or marring is minimal if any. Final touch up is common on every project. A minimal amount may be added due to handling and transportation.
Field Coating Pros:
- No freight and handling expenses. Items too large to ship.
- On site application. One can visually see what is being done onsite, although this is also changing with new technology and improved shop reports that show things in real-time and in high quality, digital spaces.
Field Coating Cons:
- Weather delays. Humidity outside of acceptable ranges is an enemy that causes delays (often ignored to meet production; however, puts proper adhesion at risk). Rain, sleet, snow, high winds, or extreme temperature are obvious delays in coating application. All of these put the project on hold until climatic conditions improve.
- Inaccessible work area. Installed substrate may not be able to be fully coated.
- Lack of workforce availability. Like it or not, getting workers to the job site is a big problem for all trades. Simply having a valid driver’s license and reliable transportation to get to the job site can be an obstacle with the workforce. Reporting to an established shop location increases worker attendance.
- Increased costs for temporary containment or special access needs. On-site storage and insurance costs can rack up the dollars. Containment structures are expensive. And that is not all. Conditioning (heating, humidity control, cooling, air quality control, negative air pressure, all rack up big overruns) is an issue.
- Schedules do not stop. Lack of painted item could delay several trades. Like dominos, everything is affected.
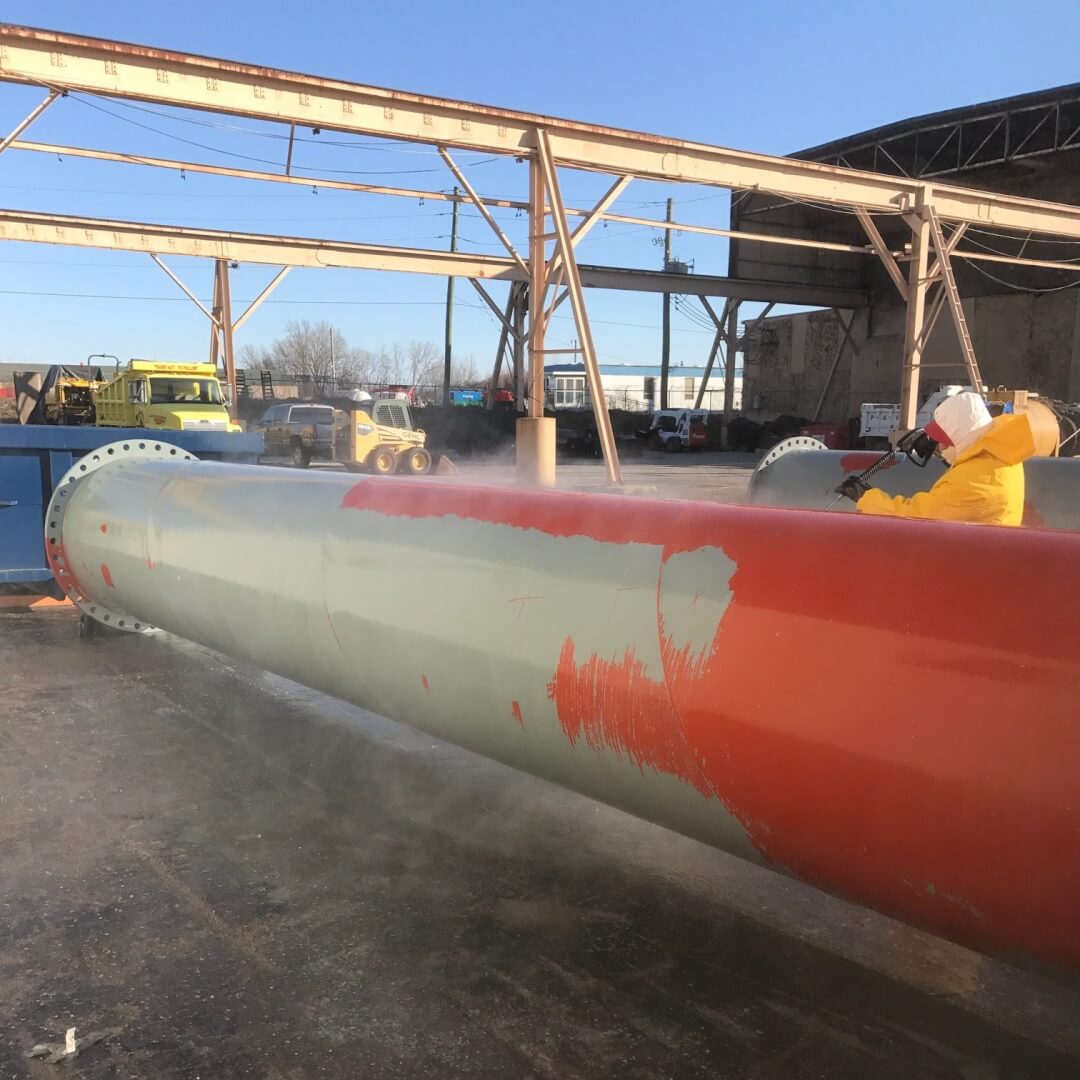
In the end, we decided to go the avenue of Shop Coating. It was clear that the specific needs of this project would be better suited to performing coatings within a controlled-climate warehouse with careful transportation in place. The result of the Deep Rock Tunnel coating was success. Had we Field Coated, in this case, there would have been far too many opportunities for coating application failure. Our goal is to extend the life of infrastructure, so each time we consider a job, we consider the long-term goals to be the primary concern. Our advice? Always find where something could go wrong when trying to decide the safest route.
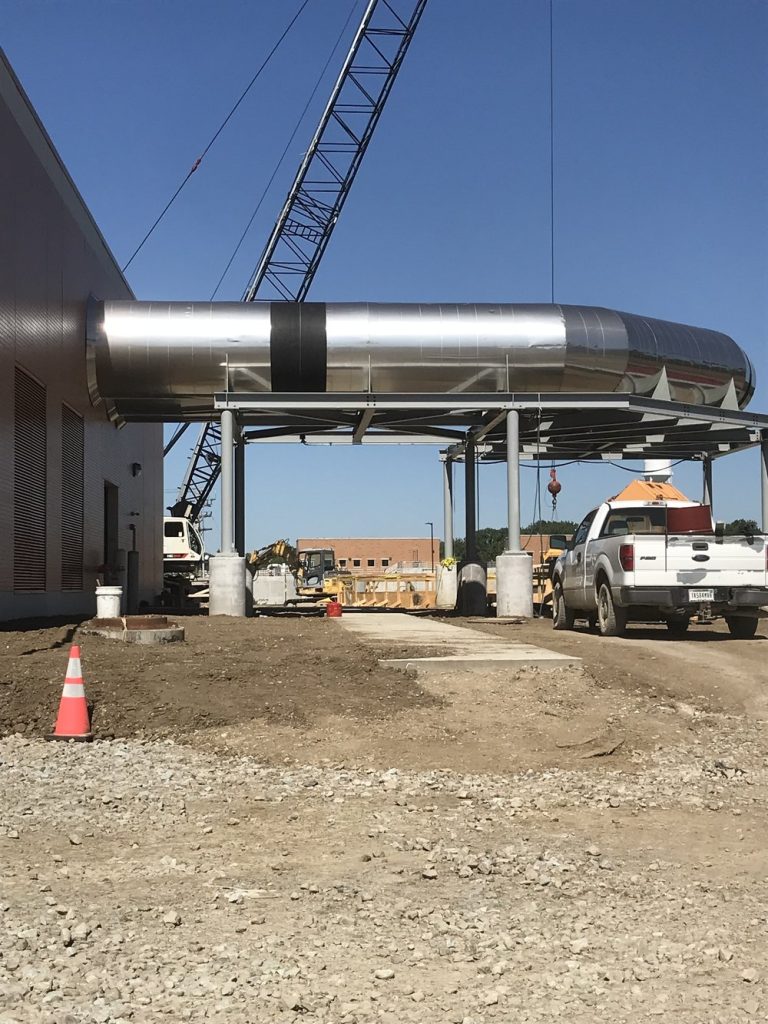

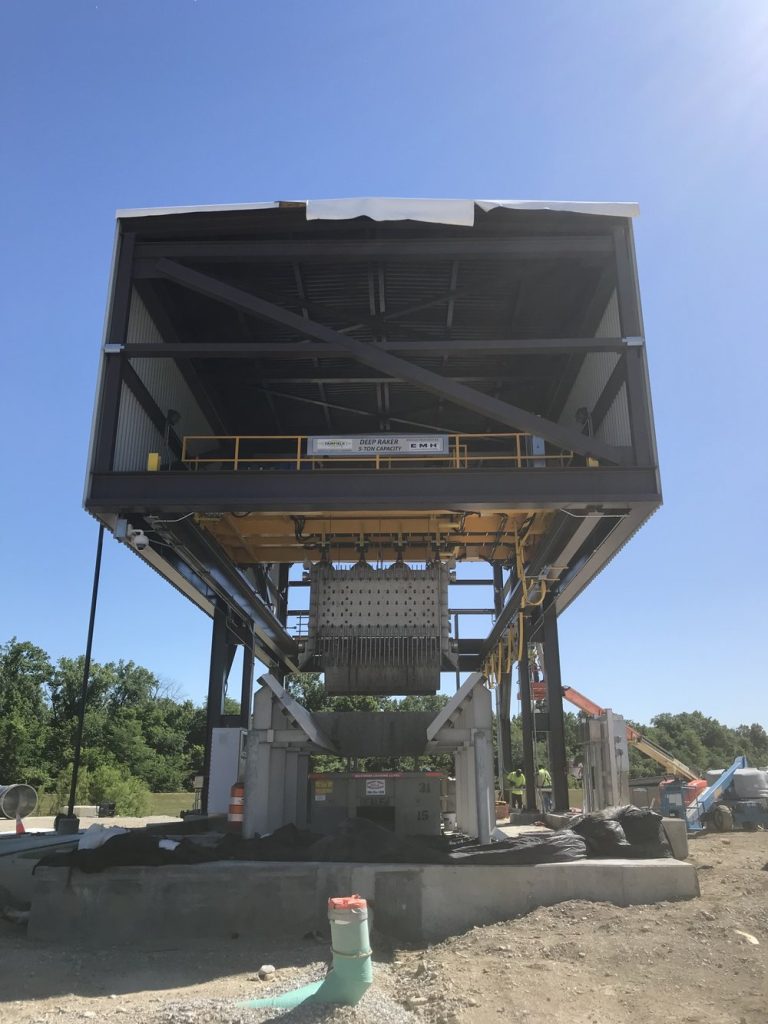
