The value of SSPC QP3 coating application is more important than ever to incorporate into every specialty coatings process. And with the start of 2018, the term “infrastructure” is resonating throughout the nation. This is the fact: Infrastructure is failing due to corrosion from coating failure.
We are embarking on a national trillion-dollar investment of replacing corroded and crumbling bridges, roadways, fences, and water/wastewater facilities. The research shows that coatings are a key element in corrosion control and we have the proven technology to extend the life of infrastructure. It is our Fiduciary Responsibility to our future generations to make decisions that are best in the long term. In this case, it is not even a difficult decision; with the facts I will present to you, I’m sure you will see how clear the beginning of the right path to better infrastructure really is.
With that said, I am presenting some solid facts with solutions as to how we can avoid coating failure while preserving and restoring the old and new.
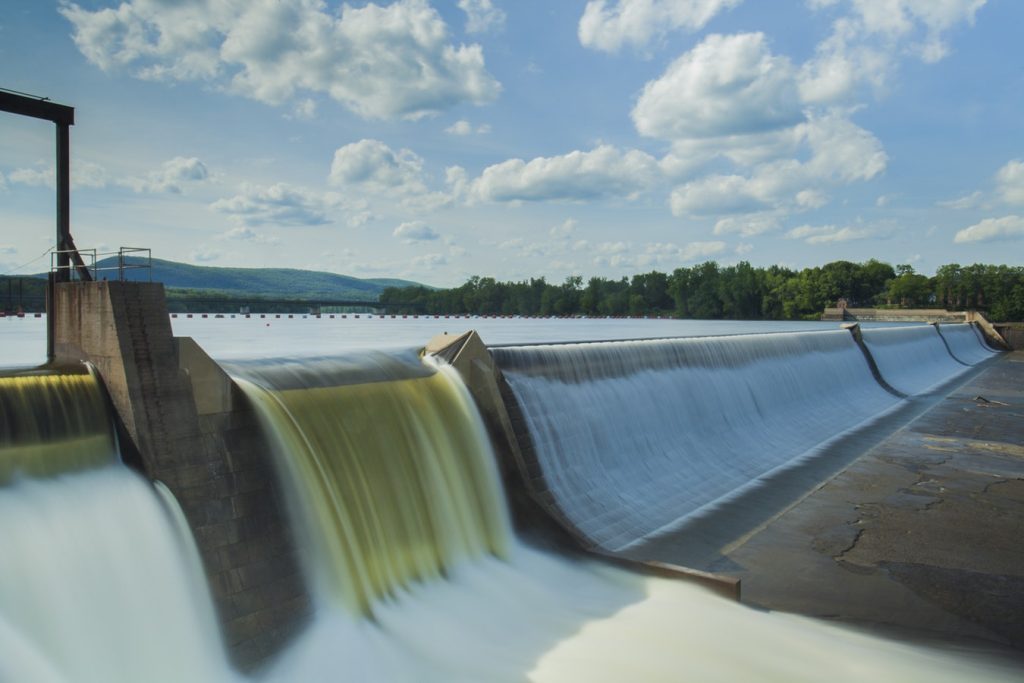
FACT: The best value is application in a controlled environment when building new or replacing old.
The cost impact for QP3 shop application is often equal to or less than field application. So often, people assume that QP3 is more expensive, but it is not. In fact, numbers show that is actually saves in the long run. The old adage “do it right the first time” rings so true in this situation; fixing mistakes months or mere years following an incorrect coating application will boost cost of the follow-up coatings to an enormous number.
FACT: Doing it right the first time, makes it easier and much more effective to do touch-ups after installation.
By design configurations, many portions of a structure become either completely inaccessible (such as feying surfaces) or extremely difficult to access. This is true for surface preparation, painting, and inspection as well. Quality is questionable at best when some areas cannot be seen by either the tradesperson or the inspector. Thankfully, engineers are placing QP3 requirement language in infrastructure specifications, which calls for higher standards in practices.

FACT: Performing specialty coating applications in the shop reduces the critical path (i.e. work schedule, timelines, etc).
This also allows the operations to be performed in a separate location while concurrent work site operations may continue without a snag. Basically, we keep the work site to the lowest possible traffic by performing as much work as possible at another location that is climate-controlled and open 24/7. Dividing up the work space in such a fashion also increases overall safety, and takes the possibilities of work site injuries to a lower level.
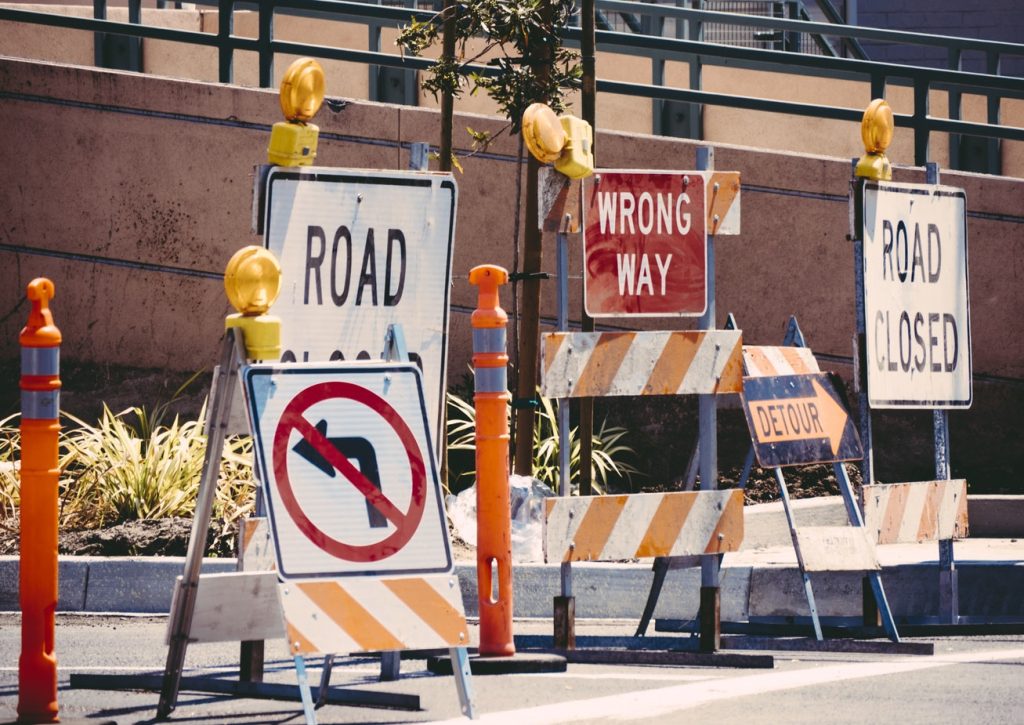
FACT: The number one coating failure is result of mistakes during surface preparation and primer application.
A controlled shop environment reduces these risks. According to a study on failure analysis, “the substrate surface is not adequately prepared for the coating that is to be applied. This may include cleaning, chemical pretreatment or surface roughening”. Weather alters schedules, introduces uncertainty and increases the odds of additional cost and failures. It affects material, equipment, prohibits work, damages finish product and work in progress alike. By performing coatings in an enclosed and industry standard environment, the risk of coating failure is reduced incredibly.
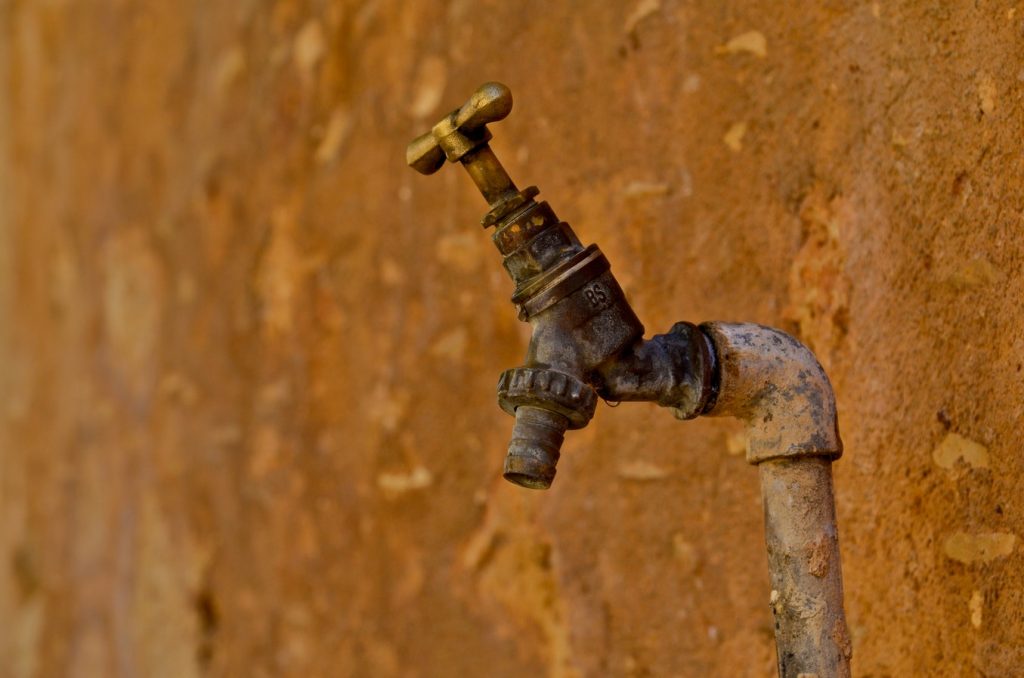
We, as Americans, stand at some major crossroads for our infrastructure. The decisions our leaders make will impact our futures as well as those of our children’s and grandchildren’s alike. We can utilize the latest technology and methods to significantly reduce corrosion and extend the life of infrastructure with SSPC QP3 Standards. Yes, we have problems with our infrastructure, but we do have solutions that we can implement starting now. And with 2018 in full swing, we can take a good step in a positive direction for the infrastructure of our country.